3DP-MAT – 3D Printed Materials for Aerospace Toolings
In this project, TUM is developing a process for hybrid composite materials, which is used to produce CFRP tools for autoclave curing in the aerospace industry.
Project Partners
GKN Aerospace GmbH, Hufschmied Zerspanungssysteme GmbH
Duration
01.04.2021 – 31.10.2023
Funding authority
Bavarian State Ministry of Economic Affairs and Media, Energy and Technology
Motivation
In the research project 3DP-MAT between GKN, Hufschmied Zerspanungssysteme GmbH and TUM, the ATLAM process (Advanced Tape Layer Additive Manufacturing) will be used to manufacture low-cost composite tools for aerospace applications. By the integration of continuous carbon fiber tapes in the printing process, the final tools achieve lower coefficients of thermal expansion (CTE) compared to only short fiber reinforced parts. A low CTE is crucial to comply with the tight tolerances required in the aerospace industry. In the project, Hufschmied is developing a modular clamping fixture. This will enable straightforward postprocessing of printed parts with different shapes to their final tolerance.
Method
Until now, 3D printing of pressure intensifiers has not been possible because the materials used in extrusion-based additive manufacturing do not have the necessary low thermal expansion and, at the same time, high temperature stability and stiffness. Other additive manufacturing processes are either unable to scale to the necessary part dimensions or also fail to achieve the necessary properties. To overcome this obstacle, the current short-fiber-reinforced 3D printing of high-performance thermoplastics will be additionally reinforced with continuous fibers. This hybrid fiber reinforcement can locally achieve the necessary material properties for use in the most demanding series production environment of aerospace curing tools for CFRP landing flaps. The material is key to opening the door for extrusion-based additive manufacturing to be used in aerospace series production. The use of 3D printed print pieces for landing flap manufacturing would be a completely new innovative approach and would almost completely eliminate the previous problems and drastically reduce the manufacturing time and cost of the print pieces. This could significantly benefit the entire landing flap production at GKN and significantly increase the efficiency of the manufacturing process.
Acknowledgement
The Chair would like to thank the Bavarian State Ministry of Economic Affairs and Media, Energy and Technology for funding the "3DP-MAT" project. – (funding code: MW-2007-0004)
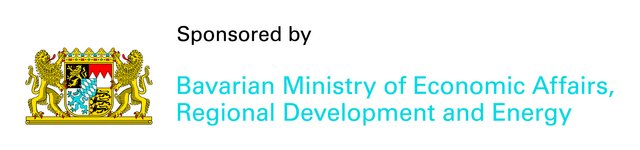
Contact Persons
Matthias Feuchtgruber, M.Sc.; Dr.-Ing. Swen Zaremba