MAI Sandwich – Development of Thermoplastically Joinable Sandwich Structures under Consideration of a Varietal Pure and Recyclable Use of Materials
Extreme lightweight design by means of new kinds of sandwich structures
Project Partners
Airbus Defence and Space GmbH, BASF SE, BMW AG, Foldcore GmbH, Neenah Gessner GmbH, Neue Materialien Bayreuth GmbH, SGL Carbon GmbH, Werkzeugbau Siegfried Hofmann GmbH
Duration
01.01.2015 – 30.06.2017
Funding authority
German Federal Ministry of Education and Research
Motivation
Sandwich structures are an essential part of modern lightweight design. They consist of a light core that is covered with skin layers on both sides. Core materials may be foams, honeycombs, thermoplastic molded parts or nub plates. As skins, preimpregnated fibrous materials (prepregs) can be used. Apart from the advantages of sandwich structures, namely high bending stiffness and dent resistance, their production is still extremely cost-intensive and time-consuming. Aditionally, the integration of functional elements such as inserts or other load bearing elements requires laborious process steps. Thus, sandwich structures are still not used in mass production. The goal of the project MAI Sandwich was therefore to develop new cost-efficient manufacturing techniques for weight-optimized sandwich structures with functional integration for use in the automotive as well as aerospace sector. The new sandwich structures had to be comprised both of a new core material and new carbon fiber-based skin layers from recycled fibers. To achieve this goal, three different processing routes under consideration of a varietal pure reuse of materials had to be investigated.
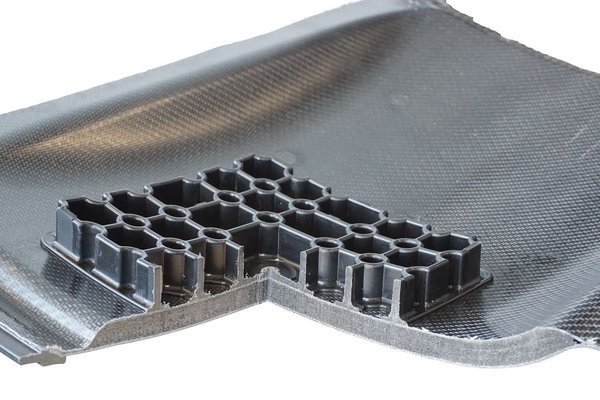
Method
The project adressed different processing routes, each with focus on a different core material. Depending on the application, automotive or aviation, high performance thermoplastics (PEEK, PEI, PESU) or technical thermoplastics (PP, PA6) were used. Moreover, the project was subdivided into there branches: Development of core systems, skin layers as well as the development of the overall process for an automated manufacturing of the thermoplastic sandwich structures under near-industrial cycle times with a focus on joining of the different layers. The results lead to the manufacturing of a three-dimensional, thermoplastic sandwich demonstrator part with an innovative core system that was overmolded at the edges and locally stiffened with an array of ribs. For this, the above-mentioned thermoplastic materials were used. Hence, a broad temperature range for heating the thermoplastic materials was reproduced. Under manufacturing aspects, the predicted cycle time of 2 minutes for automotive and 5 minutes for aviation in combination with such a high degree of complexity is remarkable. The parts were realized on a single machine at a minimum rate of scrap material without any mechanical pretreatment of the core materials (especially foam processing route). For this quantum leap regarding cost-effieient production of sandwich parts, the members of the MAI Sandwich consortium were awarded the JEC Innovation Award 2018 in the category aerospace process. The achieved results regarding manufacturing concept and predicted cycle times constitute an economically highly interesting approach for the use of sandwich structures in automotive, general mechanical or plant engineering and all the more in aviation. It is expected that this research project will sustainably promote the economic and technological acceptance of composite parts in structural applications.
Acknowledgement
The chair thankfully acknowledges the funding of the project “Entwicklung von thermoplastisch fügbaren Sandwichstrukturen unter Berücksichtigung eines sortenreinen und wiederverwertbaren Werkstoffeinsatzes – MAI Sandwich” provided by the German Federal Ministry of Education and Research under the leading-edge cluster MAI Carbon (funding code: 03MAI32X).
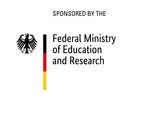
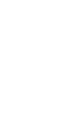
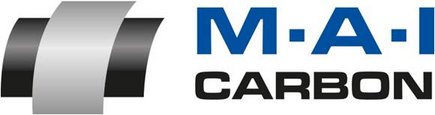
Contact Persons
Dipl.-Ing. Kalle Kind; Dr.-Ing. Swen Zaremba
Final Report
External link (pdf)